Efficient Techniques for Attaining Ideal Foam Control in Chemical Production
Efficient foam control is a critical aspect of chemical manufacturing that can dramatically affect production efficiency and product quality. By comprehending the systems of foam formation and picking appropriate anti-foaming agents, suppliers can take aggressive measures to reduce excessive foam.
Comprehending Foam Formation
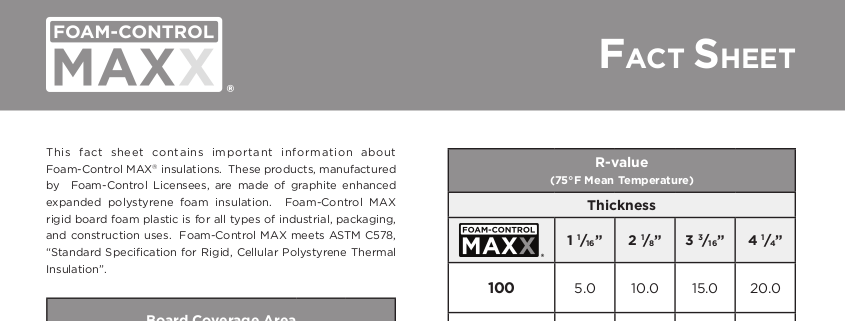
Surfactants, or surface-active representatives, decrease the surface area tension of the fluid, promoting bubble stability and promoting foam generation. Furthermore, anxiety or mixing processes can enhance bubble development, usually intensifying foam issues. The attributes of the fluid medium, consisting of viscosity and density, more impact foam behavior; for instance, more viscous fluids often tend to trap air better, bring about boosted foam security.
Recognizing these fundamental facets of foam formation is essential for efficient foam control in chemical manufacturing. By identifying the problems that promote foam advancement, producers can execute targeted techniques to alleviate its unfavorable effects, therefore maximizing manufacturing procedures and guaranteeing regular item quality. This foundational expertise is vital before checking out details methods for controlling foam in commercial settings.
Option of Anti-Foaming Representatives
When selecting anti-foaming agents, it is necessary to consider the certain characteristics of the chemical procedure and the kind of foam being created (Foam Control). Different elements affect the effectiveness of an anti-foaming agent, including its chemical structure, temperature security, and compatibility with other procedure materials
Silicone-based anti-foams are extensively used due to their high efficiency and wide temperature level array. They work by minimizing surface area stress, permitting the foam bubbles to integrate and damage even more quickly. They may not be ideal for all applications, specifically those including delicate formulations where silicone contamination is a problem.
On the various other hand, non-silicone agents, such as mineral oils or organic substances, can be useful in details scenarios, specifically when silicone deposits are undesirable. These agents have a tendency to be less effective at higher temperatures but can offer reliable foam control in various other conditions.
In addition, understanding the foam's beginning-- whether it emerges from aeration, anxiety, or chain reactions-- guides the choice process. Testing under actual operating conditions is important to ensure that the chosen anti-foaming agent meets the special demands of the chemical manufacturing procedure efficiently.
Process Optimization Techniques
Reliable foam control is an important element of maximizing chemical manufacturing procedures. By fine-tuning these specifications, drivers can minimize disturbance, therefore minimizing foam formation during blending.
Furthermore, managing temperature and stress within the system can substantially influence foam generation. Decreasing the temperature level might lower the volatility of particular parts, leading useful reference to lowered foam. Maintaining ideal stress degrees assists in reducing excessive gas release, which adds to foam security.
Another efficient strategy is the tactical addition of anti-foaming representatives at crucial stages of the process. Mindful timing and dosage can make certain that these representatives properly suppress foam without disrupting various other process parameters.
Additionally, integrating a systematic analysis of basic material homes can aid identify naturally foaming compounds, enabling preemptive actions. Performing routine audits and process evaluations can disclose inadequacies and locations for renovation, making it possible for continual optimization of foam control methods.
Surveillance and Control Systems
Surveillance and control systems play a critical duty in keeping ideal foam administration throughout the chemical production process. These systems are essential for real-time observation and adjustment of foam degrees, making certain that production efficiency is taken full advantage of while minimizing interruptions brought on by excessive foam development.
Advanced sensing units and instrumentation are used to detect foam density and height, offering important information that notifies control algorithms. This data-driven approach enables for the prompt application of antifoaming representatives, making sure that foam degrees continue to be within appropriate restrictions. By integrating tracking systems with process control software program, producers can carry out automated reactions to foam variations, reducing the requirement for manual treatment and boosting operational consistency.
Moreover, the assimilation of artificial intelligence and anticipating analytics into checking systems can promote positive foam administration. By evaluating historic foam information and functional criteria, these systems can anticipate foam generation patterns and suggest preemptive steps. Regular calibration and upkeep of surveillance equipment are important to make certain accuracy and reliability in foam detection.
Eventually, reliable monitoring and control systems are important for enhancing foam control, advertising safety and security, and improving general performance in chemical manufacturing settings.
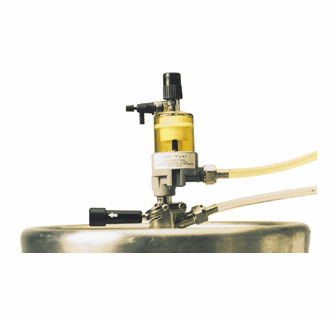
Study and Ideal Practices
Real-world applications of tracking and control systems highlight the importance of foam management in chemical manufacturing. A notable case study includes a large pharmaceutical producer that executed an automated foam detection system.
Another exemplary instance originates from a petrochemical see it here business that adopted a combination of antifoam representatives and procedure optimization methods. By analyzing foam generation patterns, the company tailored its antifoam dose, resulting in a 25% reduction in chemical usage and substantial cost savings. This targeted method not just decreased foam interference yet additionally improved the general security of the production process.
Verdict
In conclusion, accomplishing optimal foam control in chemical manufacturing requires a thorough method including the selection of suitable anti-foaming agents, application of procedure optimization methods, and the assimilation site here of advanced monitoring systems. Regular audits and training additionally boost the efficiency of these methods, fostering a culture of continual improvement. By addressing foam development proactively, suppliers can considerably improve production efficiency and product quality, ultimately adding to even more affordable and sustainable procedures.
By recognizing the devices of foam development and choosing ideal anti-foaming agents, producers can take positive measures to reduce excessive foam. The qualities of the fluid medium, including viscosity and thickness, more influence foam behavior; for example, even more viscous liquids often tend to trap air extra effectively, leading to increased foam stability.
Understanding these fundamental aspects of foam development is crucial for efficient foam control in chemical production. By assessing historical foam information and operational criteria, these systems can anticipate foam generation patterns and advise preemptive steps. Foam Control. Regular audits of foam control determines guarantee that procedures remain enhanced, while fostering a culture of positive foam monitoring can lead to lasting renovations throughout the production range